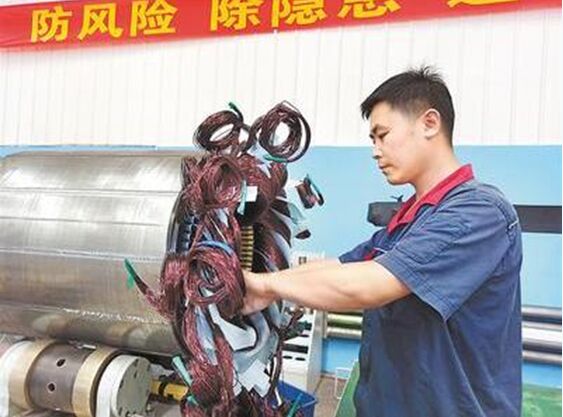
9月1日,河北電機股份有限公司員工正在變頻高效高壓電機數字化車間進行電機生產。
9月1日,走進位于石家莊市欒城區的河北電機股份有限公司變頻高效高壓電機數字化車間,只見車間內上料、生產、組裝、噴涂各道工序都在緊張有序進行。 在車間的定子嵌線區,公司員工武海輝正在通過智能終端掃描線圈上的條碼。顯示屏上,線圈信息和他需要進行的工作一一顯示。他告訴記者:“以前原材料尋找、交接,工作布置需要較長時間。進行數字化改造后,這些環節變得很順暢。” 瞄準全球供應鏈高端市場,河北電機是生產超高效節能電機、專用特種電機產品的電機專業制造企業,為壓縮機、水泵、制冷、減速機、電梯、印染等行業國際領先企業提供產品和服務,產品出口美國、加拿大等20多個國家和地區。 他們發現,大中型電機制造逐漸向單機容量大、特殊化、多樣化、定制化方向發展,且變頻調速技術產業化還不夠理想。2016年開始,他們開展了變頻高效高壓電機數字化車間建設,加大變頻高效高壓電機生產。該項目于2018年全部完成。 如今,漫步在車間,只見監測設備密布于生產線各節點,10多個智能終端對應著不同的工位,從德國進口的生產設備正在進行定制化產品生產。 “數字化改造花費了900多萬元,加上這些制造設備,整個車間投資總額接近1億元。這個車間展示了我們最先進的制造水平。”河北電機IT中心主任石欣介紹,車間實現數字化,首個環節是把企業資源計劃(ERP)、制造執行系統(MES)、分布式控制系統(DCS)三個系統進行融合。這也是整個過程的難點所在。 ERP負責外部訂單處理和庫房物料管理,DCS負責底層各類設備的聯網與通信,MES負責車間現場執行過程管控,對上接收ERP訂單數據,對下集成DCS系統,實現設備連接與控制指令下發。 通過和來自北京、南京的技術團隊進行聯合攻關,他們確定了三系統的融合方案:不同系統之間采用先進的WEB服務作為統一集成接口,方便相互調用;數據統一采用標準格式,便于解析和交換,提高傳輸效率。經過大量試驗,系統終于實現了有機融合。 數字信息的實時獲取也是數字化改造的關鍵。 在這方面,他們通過在生產線和車間的各關鍵工位和節點設置多個信息采集點,實現了智能感知和在線監測。 兩個關鍵步驟和一些后續環節完成后,車間就實現了“管控一體化”:經營計劃、采購、物料、生產、庫存、銷售、財務等實現了動態監控。同時,車間的物流、信息流、控制流和資金流實現“四流合一”。 如今,在這個車間,刷一下卡就能知道自己該做什么。 結合MES、PDM(產品數據管理)、ERP系統,數字化車間實現了電子工單自動發放到工位,工人在電子終端上刷卡就能接收到當班工作任務,圖紙和作業指導書也會跟隨工單同時下發。 變化不止于此。 通過ERP和MES,車間實現了物料按工位揀選配送,通過條碼等工具,配送過程實現了高效、精確。 車間也變得透明。通過網絡、傳感器、智能終端,車間實現了對設備、物料、人員等車間現場信息的實時采集,實現生產過程透明化。 管理者也能體會數字化帶來的便利。車間的生產進度、工時統計、質量狀況、設備運行狀況等數據經過組織梳理后,能夠根據需要的樣式,以報表、統計圖等方式在監控大屏上進行展示,實時反映車間的生產狀況,便于生產主管及時掌握作業情況。 “變頻高效高壓電機數字化車間建成后,生產過程實現可視、可控,產品實現了可追溯,產品質量、生產效率均得到大幅提高。”該公司變頻高效高壓電機數字化車間項目經理范立欣介紹。相比以前,數字化車間生產效率提高20%,運營成本降低15%,產品生產周期縮短30%,產品不良率降低15%。車間每年為企業節省600萬元成本,增加約1000萬元銷售額。 在該車間,記者看到,來自阿特拉斯、英格索蘭、格蘭富、西門子等國際巨頭的訂單產品正在緊張生產。通過數字化車間建設,河北電機產品的競爭力得到大幅提高,訂單不斷。
|